For years, WORD Rock Drills has been at the forefront of providing high-quality rock drilling attachments to the fencing community. With a range of skid steer drilling options catering to various needs, WORD has been a trusted partner for fence installers nationwide. Recognizing a gap in the market and the evolving needs of our customers, we are thrilled to unveil our latest innovation: the WORD DTH Auger Drive Kit.
Revolutionizing Rock Drilling for Fence Installers
Designed to address the specific challenges faced by fence installers dealing with tough soil conditions, the DTH Auger Drive Kit is a game-changer in the industry. This new kit allows for shallow hole drilling of up to 6 feet deep and 6 inches wide, empowering installers to take on more challenging projects with confidence.
Key Features and Benefits of the WORD DTH Auger Drive Kit
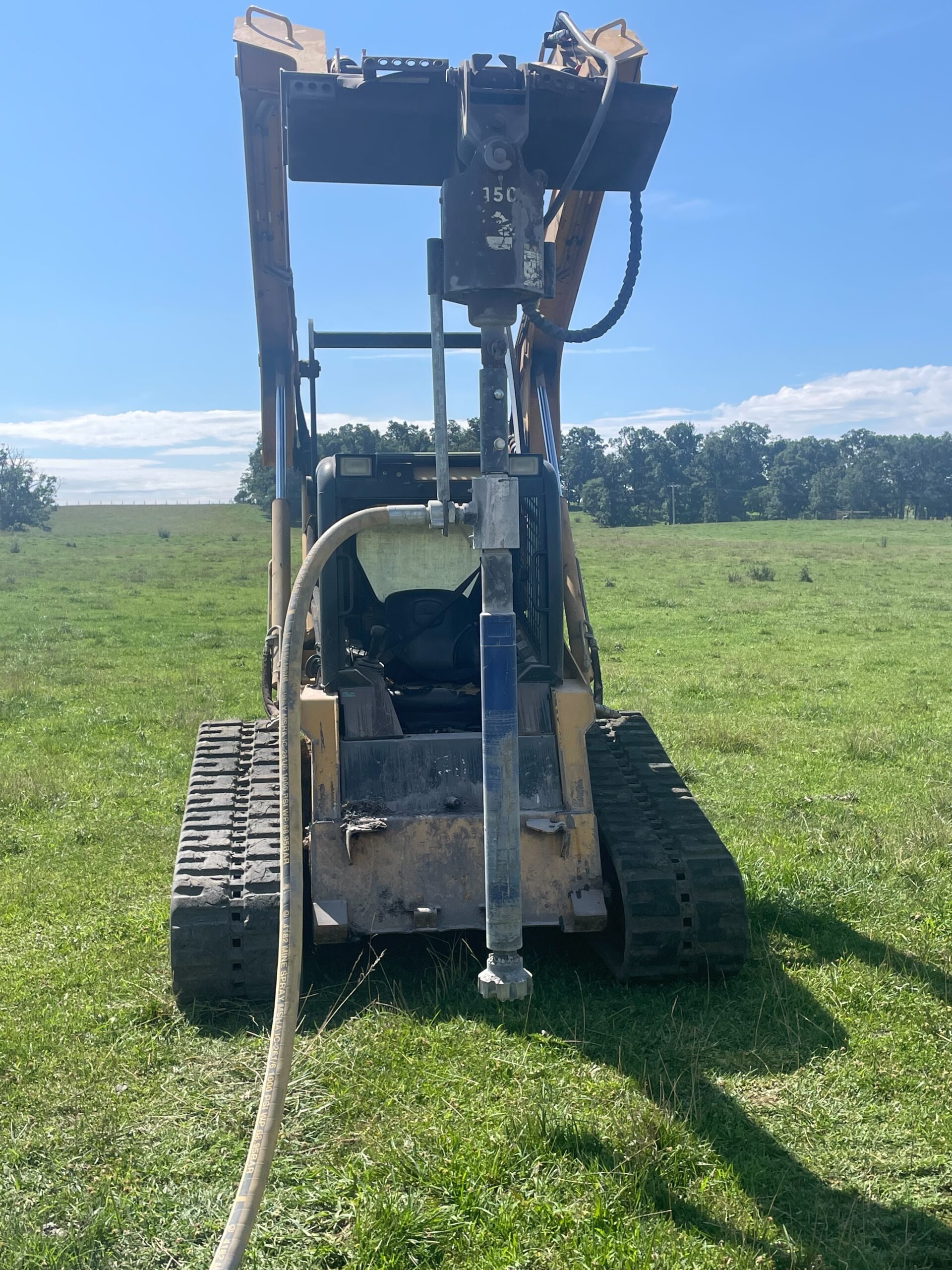
What sets the WORD DTH Auger Drive Kit apart is its user-friendly design and efficiency. Installers can now convert their existing Auger Drive Head into a powerful rock drill. This kit eliminates the need for subcontracting drilling services or costly excavation processes. This not only saves valuable time but also significantly reduces project costs, making it a cost-effective solution for businesses of all sizes.
WORD Salesman, Reid Sockwell, has worked closely with fencing customers for many years and has seen several thrive with this new product line. “I had many customers who were unsure about investing in our standard skid steer attachment but needed a drilling solution. Traditional methods were costing them time and money, but they weren’t ready to make the leap to one of our larger attachments. The DTH Auger Drive Kit met them halfway, helping them win contracts and complete work quickly.” – Reid Sockwell
Versatility and Integration
One of the key advantages of this kit is its versatility. By incorporating a tool familiar to many fencing installers—the Auger Drive Head—WORD has created a solution that seamlessly integrates into existing workflows. Whether you’re working on residential fencing projects or commercial installations, this kit is engineered to meet your drilling needs efficiently and effectively. Adaptable to a range of auger drive heads from Digga, Pro-Dig, Eskridge, Eterra, Pengo, and more, the WORD Auger Drive Kit is a flexible solution to help fencing installers meet their goals.
Compact and Portable
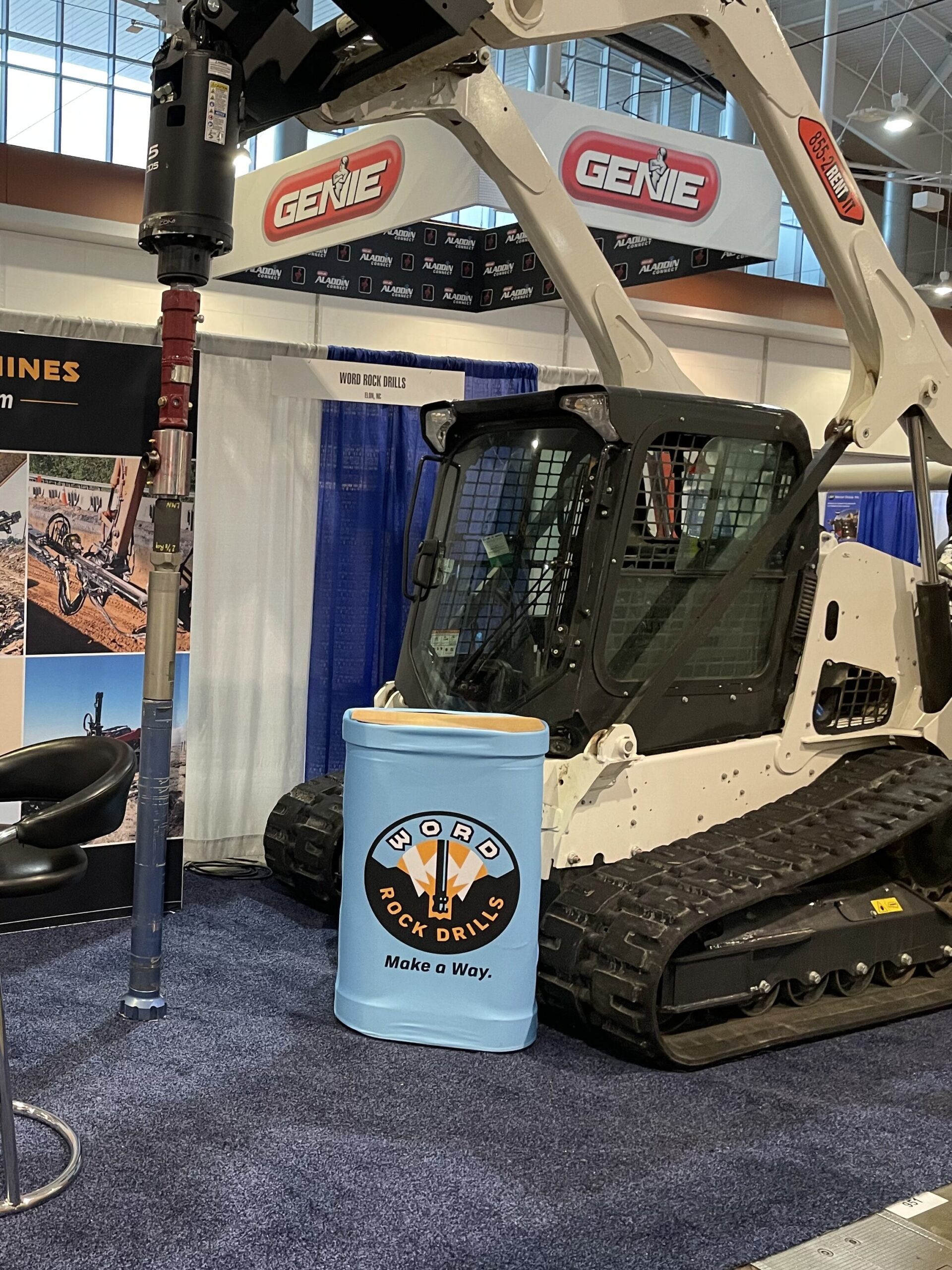
The compact nature of the DTH Auger Drive Kit means it can be easily transported and maneuvered on-site. Unlike the WORD SS Series Drill Attachment used for larger commercial-scale fencing installations, the smaller footprint of the DTH Auger Drive Kit enhances maneuverability and overall productivity for smaller sites. With this tool in your fleet, you can take on challenging terrains and expand into new markets with confidence.
Commitment to Innovation and Customer Satisfaction
At WORD, we believe in not just meeting but exceeding our customers’ expectations. The development of the DTH Auger Drive Kit is a testament to our commitment to innovation and customer satisfaction. We invite fence installers everywhere to experience the difference firsthand and revolutionize their rock drilling capabilities.
The WORD DTH Auger Drive Kit is not just a product; it’s a solution that empowers fence installers to overcome obstacles, save costs, and achieve greater efficiency in their operations. Discover the future of rock drilling with WORD Rock Drills today!
Learn More at https://www.wordrockdrills.com/product/dth-auger-drive-kit/